5 Effective Ways to Reduce Inventory Surplus
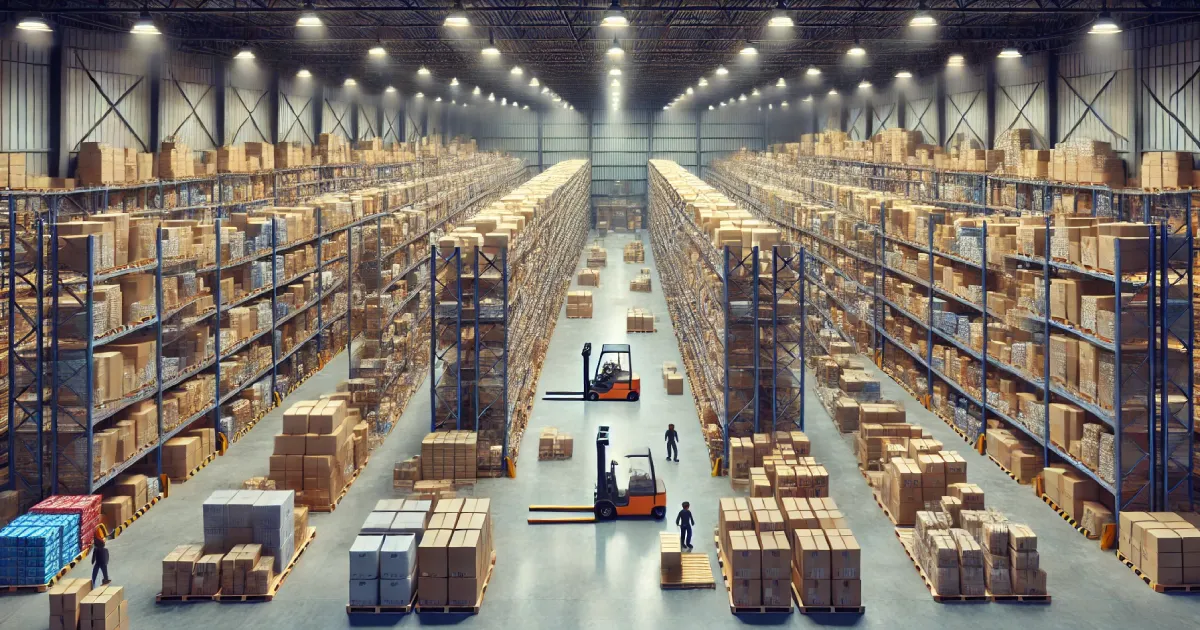
Many companies grapple with the issue of excess stock, regardless of their industry. This surplus inventory problem extends beyond just tying up financial resources; it also inflates storage expenses and risks product obsolescence. Efficiently managing stock levels is thus crucial for trimming excess and streamlining business operations.
This piece explores a set of 5 time-tested approaches that organizations can employ to tackle surplus inventory and boost their operational effectiveness. By implementing these strategies, businesses can free up capital, reduce costs, and enhance their overall performance.
Understanding Inventory Surplus
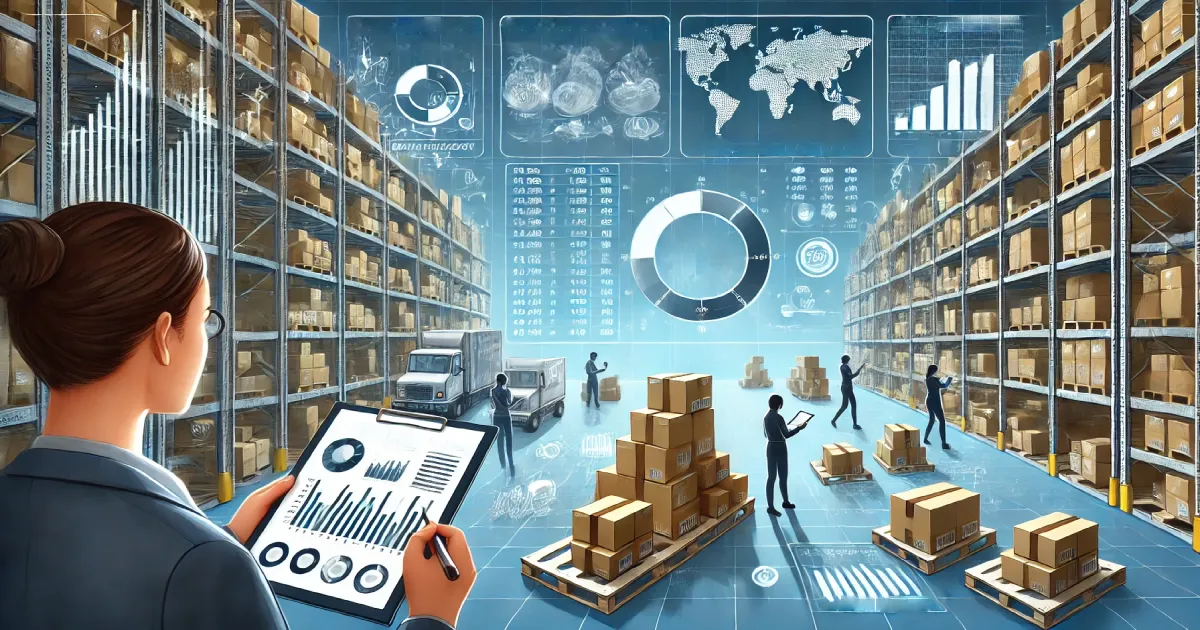
Definition and Causes
Inventory surplus occurs when the stock levels of products exceed the demand. This can be due to various factors, including inaccurate demand forecasting, over-ordering, seasonal fluctuations, and changes in consumer preferences. Understanding the root causes of surplus inventory is the first step towards addressing the issue effectively.
Impact on Business
Surplus inventory can have several adverse effects on a business, including:
- Increased Holding Costs: Storing excess inventory incurs costs related to warehousing, insurance, and handling.
- Cash Flow Constraints: Capital tied up in surplus inventory could be used more effectively elsewhere in the business.
- Obsolescence Risk: Products may become obsolete before they are sold, leading to potential write-offs and losses.
- Storage Space Issues: Excess inventory occupies valuable warehouse space that could be used for other purposes.
Method 1) Demand Forecasting and Planning

Importance of Accurate Forecasting
Accurate demand forecasting is crucial for maintaining optimal inventory levels. By predicting future demand, businesses can adjust their inventory purchases accordingly, reducing the risk of surplus. Effective forecasting involves analyzing historical sales data, market trends, and other relevant factors.
Tools and Techniques for Effective Forecasting
Several tools and techniques can aid in accurate demand forecasting:
- Time Series Analysis: Analyzes historical data to identify patterns and trends.
- Causal Models: Use external variables (e.g., economic indicators) to predict future demand.
- Qualitative Methods: Involves expert opinions and market research.
Case Study: Successful Implementation
A mid-sized retail company successfully reduced its inventory surplus by implementing a sophisticated demand forecasting system. By leveraging time series analysis and integrating it with market trend data, the company achieved a 20% reduction in surplus inventory within six months.
Method 2) Inventory Optimization Techniques

Just-In-Time (JIT) Inventory
JIT inventory management involves receiving goods only when they are needed in the production process, thereby reducing holding costs and minimizing surplus. This technique requires a reliable supply chain and efficient logistics.
ABC Analysis
ABC analysis categorizes inventory into three classes:
- A Items: High-value products with low sales frequency.
- B Items: Moderate value and sales frequency.
- C Items: Low-value products with high sales frequency.
By focusing on A items and managing them more closely, businesses can reduce excess inventory more effectively.
Economic Order Quantity (EOQ)
EOQ is a formula used to determine the optimal order quantity that minimizes total inventory costs, including ordering and holding costs. Implementing EOQ can help businesses maintain optimal inventory levels and reduce surplus.
Method 3) Regular Inventory Audits and Reviews

Benefits of Regular Audits
Conducting regular inventory audits helps identify surplus stock, discrepancies, and areas for improvement. Audits ensure that inventory records are accurate and up-to-date, facilitating better decision-making.
Steps to Conduct Effective Inventory Reviews
- Plan the Audit: Define objectives and scope.
- Count Inventory: Conduct physical counts of stock.
- Reconcile Discrepancies: Compare physical counts with records and address discrepancies.
- Analyze Data: Identify patterns and areas for improvement.
Real-World Examples
A leading electronics retailer conducted quarterly inventory audits, leading to a 15% reduction in surplus inventory within a year. The audits helped identify slow-moving items and optimize reorder points.
Method 4) Leveraging Technology for Inventory Management

Role of Inventory Management Software
Modern inventory management software offers features like real-time tracking, automated reordering, and analytics. These tools help businesses maintain optimal inventory levels and reduce surplus.
Integrating AI and Machine Learning
AI and machine learning algorithms can predict demand more accurately by analyzing large datasets and identifying patterns. These technologies can optimize inventory management processes and reduce surplus.
Success Stories from Industry Leaders
Several industry leaders have successfully reduced surplus inventory by leveraging technology. For instance, a global e-commerce giant implemented AI-driven demand forecasting, resulting in a 30% reduction in surplus inventory.
Method 5) Strategic Supplier and Vendor Management

Building Strong Supplier Relationships
Strong relationships with suppliers can lead to more flexible terms and better collaboration. Regular communication and collaboration with suppliers can help align inventory levels with actual demand.
Vendor-Managed Inventory (VMI)
VMI involves suppliers managing inventory levels on behalf of the business. This reduces the burden on the business and ensures that inventory levels are optimized.
Negotiating Flexible Terms
Negotiating flexible terms with suppliers, such as smaller order quantities or more frequent deliveries, can help reduce surplus inventory. Flexibility in terms can align inventory more closely with actual demand.
Final Thoughts
Minimizing excess stock is crucial for optimizing operations and boosting profits. Companies can substantially cut down on surplus inventory by enhancing demand predictions, refining inventory management, conducting frequent stock checks, adopting advanced technology, and improving supplier relationships.
These approaches offer multiple benefits beyond just reducing excess inventory. They unlock tied-up funds, lower storage expenses, and streamline overall business processes. By implementing these strategies, businesses can achieve greater operational efficiency and improve their bottom line.
Key Takeaways
Method | Key Takeaways |
---|---|
1. Demand Forecasting and Planning | - Accurate forecasting is crucial. - Use tools like time series analysis. - Improved forecasting can reduce surplus by 20%. |
2. Inventory Optimization | - Just-In-Time (JIT) reduces holding costs. - ABC analysis focuses on high-value items. - Economic Order Quantity (EOQ) minimizes costs. |
3. Regular Inventory Audits | - Audits identify surplus and discrepancies. - Steps: plan, count, reconcile, analyze. - Quarterly audits reduced surplus by 15%. |
4. Leveraging Technology | - Software offers real-time tracking and automated reordering. - AI improves forecasting accuracy. - AI-driven forecasting reduced surplus by 30%. |
5. Supplier and Vendor Management | - Strong supplier relationships and flexible terms help. - Vendor-Managed Inventory (VMI) optimizes stock. - Negotiating terms aligns inventory with demand. |
Frequently Asked Questions (FAQs)
Q1: What is inventory surplus?
Inventory surplus occurs when the stock levels of products exceed the demand, leading to excess inventory.
Q2: How does surplus inventory impact a business?
Surplus inventory increases holding costs, ties up capital, risks obsolescence, and occupies valuable storage space.
Q3: What is demand forecasting?
Demand forecasting involves predicting future demand for products based on historical data, market trends, and other factors.
Q4: How can technology help in reducing surplus inventory?
Technology, such as inventory management software and AI-driven demand forecasting, helps optimize inventory levels and reduce surplus.
Q5: What is Vendor-Managed Inventory (VMI)?
VMI is a practice where suppliers manage inventory levels on behalf of the business, ensuring optimal stock levels.