Inside the World’s Largest 3D-Printed Neighborhood
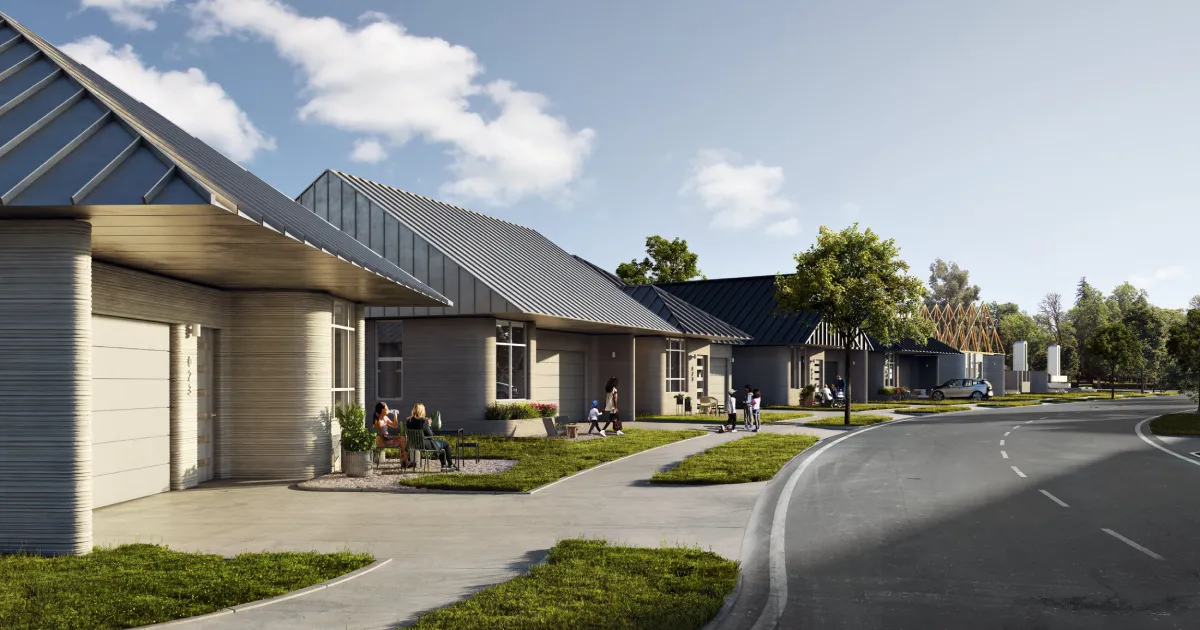
Just outside Austin, in the fast-growing suburb of Georgetown, Texas, a quiet revolution in homebuilding is underway. What looks like a conventional neighborhood at first glance reveals itself to be a groundbreaking innovation in construction: the world’s largest 3D-printed housing community.
This futuristic development is the result of a partnership between Lennar, the nation’s second-largest homebuilder, and Icon, a 3D technology company known for pushing the boundaries of construction. Together, they’ve built 100 homes using massive robotic printers that extrude layers of concrete, creating the walls with rounded edges and a texture reminiscent of wide-wale corduroy.
Two years in the making, the project—part of the Wolf Ranch master-planned community—has already seen about 75% of its homes sold. The houses, available in 2- and 3-bedroom layouts, are priced just under $400,000 and come with the full suite of amenities found in any other Lennar development. What makes them different, however, is their construction method, energy efficiency, and durability.
Each home is solar-powered, and thanks to concrete’s natural insulation, residents are already seeing dramatic reductions in utility costs. Holly Feekings, a retiree who moved in a year ago, reported a $26 electric bill last month. “I feel safer in this house than any house I’ve ever lived in,” she said. “It’s not going to burn down.”
Pierre Megie, another homeowner in the community, was drawn to the design and efficiency. “It had everything: tall doors, taller ceilings, cement floors. A combination of energy efficiency, practicality, the price point—and the aesthetics.”
The construction process itself is nothing short of remarkable. Icon started the build with two 40-foot robotic printers in 2022 and scaled up to 11 machines within a year. Operating 24/7, these printers can produce two homes per week, effectively replacing the labor of a dozen workers per unit. The only part not printed is the roof, which in this case is made of metal.
According to Icon CEO Jason Ballard, building at scale was crucial to proving the technology’s viability. “The truth is in the field, not in the lab,” he said. Collaborating with Lennar required figuring out how to integrate robotic printing with traditional construction workflows—everything from pouring foundations to finishing interiors.
While the initial costs ran slightly higher than expected, Lennar’s chairman and co-CEO Stuart Miller said the lessons learned have already driven costs and build times down significantly. “We’ve seen our costs go down by half. We’ve seen our cycle time go down by half,” he said.
That learning curve is now fueling a second, even more ambitious project: a 200-home 3D-printed community in Texas. This next phase promises larger homes at a lower cost, constructed more quickly thanks to efficiencies gained in Georgetown.
With housing affordability a growing issue across the U.S., the implications are huge. 3D printing could not only streamline construction and reduce costs but also create more resilient homes—better able to withstand fires, hurricanes, and other environmental threats. And since all concrete used by Icon is sourced domestically, potential trade tariffs won't slow progress.
What started as an experiment is quickly proving to be a scalable solution for the future of housing—durable, efficient, and beautifully unconventional.